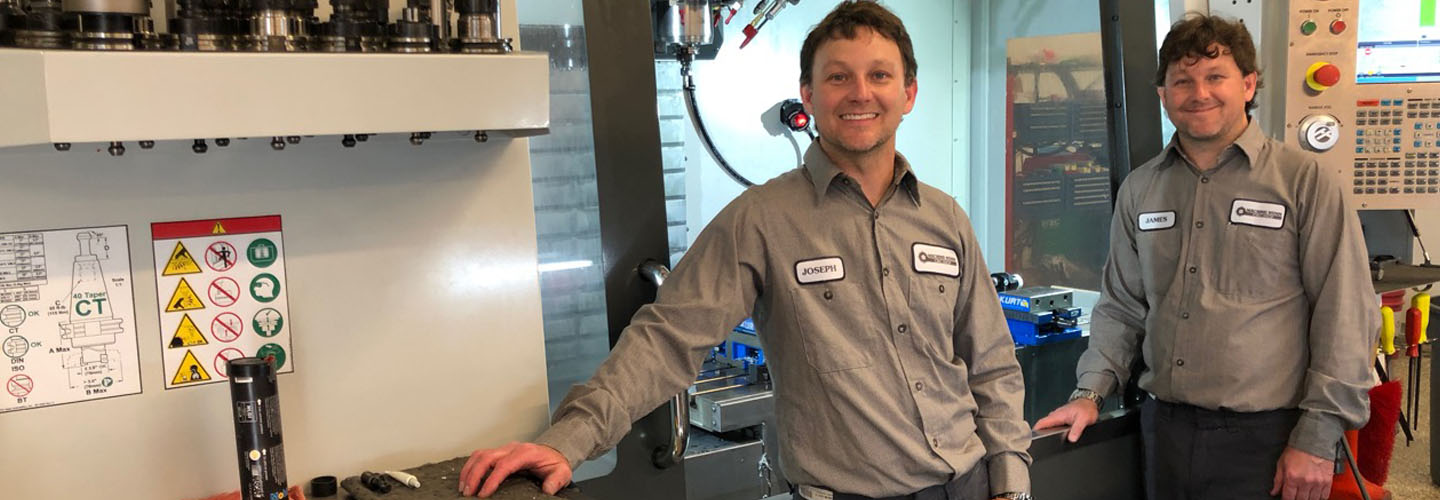
Machining High-Quality Parts is Now What’s Driving the Nunn Brothers
After nearly 20 years working the pits at NASCAR race tracks and race shops, building and maintaining high-speed race cars, brothers James and Joseph Nunn opened their own machine shop in 2015 in a 6,000-square-foot building James and his wife Shelly built in Statesville, NC. While the Nunns’ knew enough machining to get started, they also knew that they needed to invest in the right machines to be competitive in a tough market and powerful software that could optimize the machines’ power, maximizing output and accuracy, and giving them a respectable reputation as machinists.
Quick Facts:
Product Used: Dynamic Milling
Industry: Aerospace and Defense, Consumer, Tool & Die
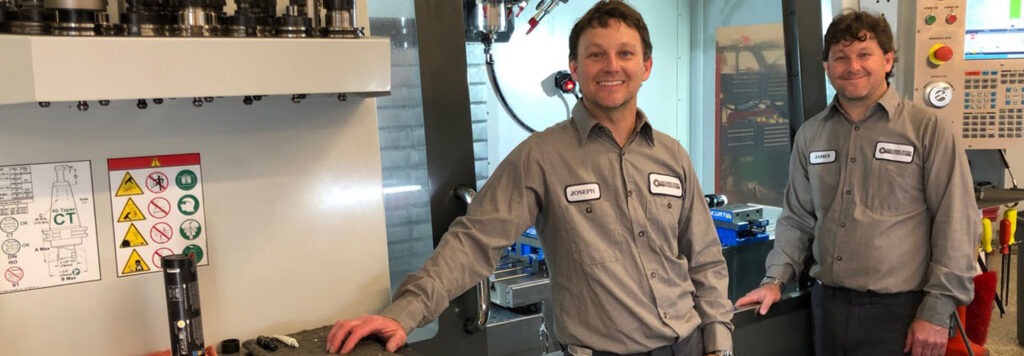
PROJECT DETAILS
- The Challenge: Optimize the manufacturing operations of a start-up job shop with stiff competition and owners that are new to the art of CAD/CAM programming.
- The Solution: Mastercam CAD/CAM Software
- Benefits:
- An easy-to-learn user interface enables those new to program to learn intuitively and quickly.
- Powerful Dynamic Motion technology removes material quickly so that complex jobs can be quoted on and completed in short times.
- The Tool Library reduces the time it takes to specify tools for each job, saving significant time, and ensuring an accurate tool selection.
- Having a dedicated Reseller that not only knows how to help with problems along the way but will take the time to teach the software properly.
Machine Nunn produces high quality parts for motorsports, government/military projects, and gun manufacturers. “We’re really more of a job shop,” James said, “making anywhere from one to 2,000 parts for any one of our customers.” Machine Nunn operates all Haas equipment including the VF2 3-axis CNC vertical mill, the ST20Y Y-axis CNC lathe, and VF4 3-axis CNC vertical mill. At the end of 2018, they added another Haas lathe, the ST15.
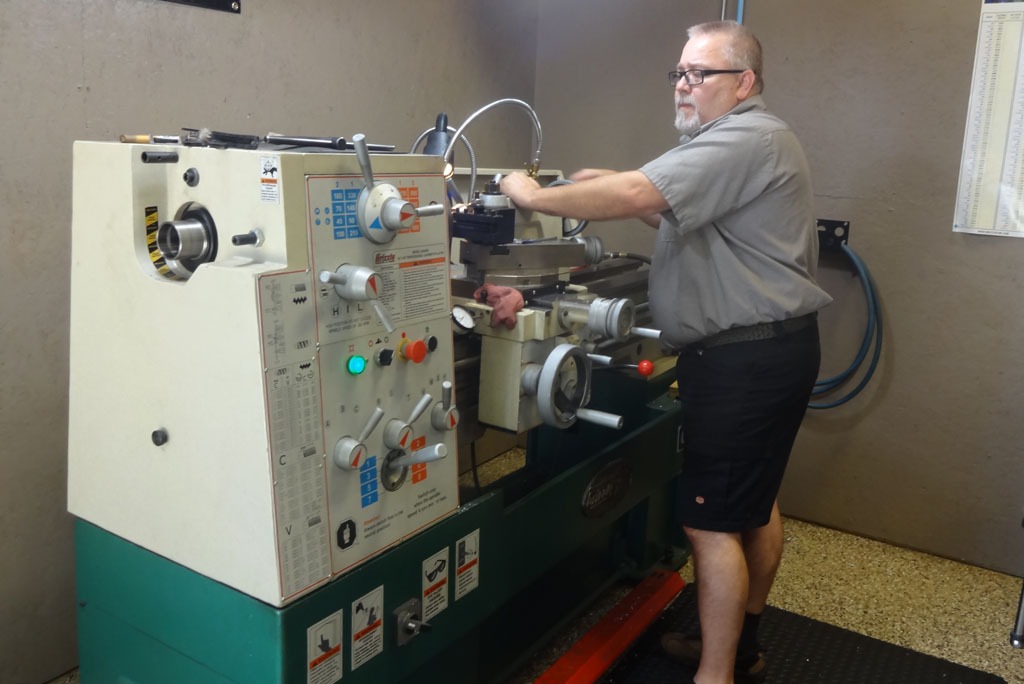
“We machine parts that are smaller than a penny, to something like I’m working on right now in the mill that’s 11½” diameter,” said James. Recently, they made a 48”x-36” fixture plate for Zac Brown’s Southern Grind (Peachtree City, GA), the high-end knife company owned by singer Zac Brown, James said.
Machine Nunn works with tolerances ranging from a +/-0.0005” up to +/-0. 010”. To program their CNC machines, Machine Nunn uses Mastercam CAD/CAM software.
“Mastercam was the clear choice for us,” James said. “It’s perfectly suited to our needs.” The Nunn Brothers reached out to their Mastercam Reseller, Barefoot CNC, located in Morganton, NC. For the better part of the next year, Barefoot Applications Engineer Jason Parks spent Saturdays, Sundays, and late into many weeknights training James on the software.
“I did everything I could do to move through the learning curve,” James said. “I took 10 online instruction classes which were helpful. But it was really sitting beside Jason day after day that helped me. I had my own personal Mastercam teacher and I became ‘a sponge’. Everything Jason could show me, he showed me. Everything I could take in, I took in. Sometimes I’d get it the first time, sometimes it would take two or three tries, but I was persistent.”
James especially likes Dynamic Milling. “It just does everything for you,” he said. He explains, “We have a part that is 11” around and the stock is 11 ½” with part of the circle going into 6” or 7”. Instead of doing a contour with multiple paths and having to figure out the math, the number of passes, the step-overs, and feeds and speeds, I just programmed a Dynamic toolpath and said, “My part is this big and I’m going to this size and I only want to step over this much, and I don’t want to hit this part, but I do want to cut from here.”
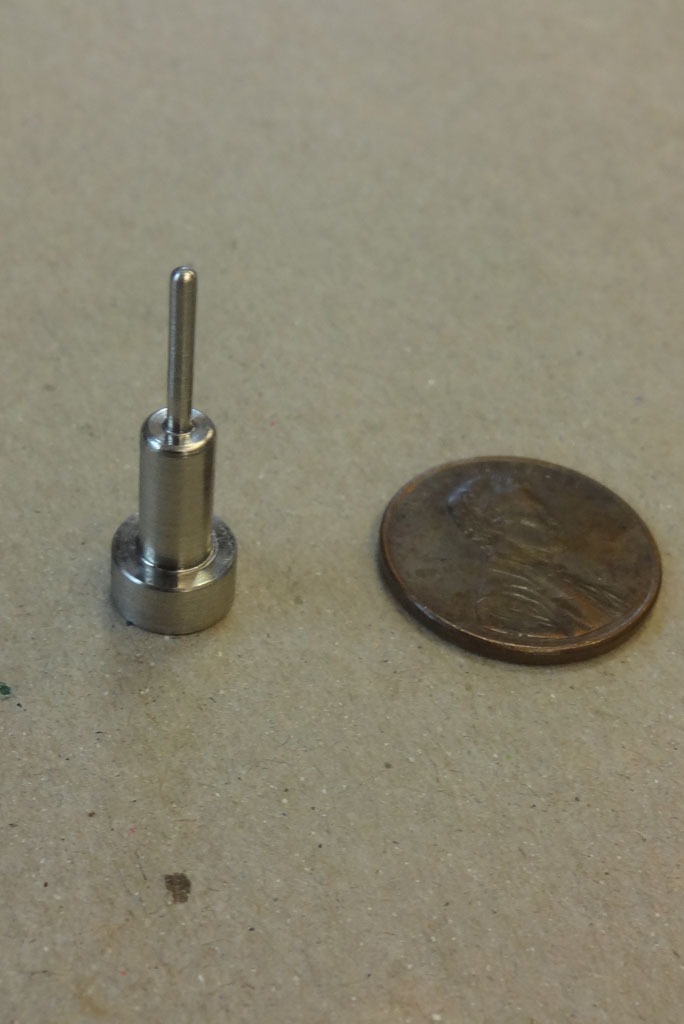
James continues, “And you just enter the numbers, click on the lines that you want to cut from and to, define the avoidance region with a cut from, a step over, a feed and speed, and you tell it how deep to go…And—boom!—there’s your toolpath,” he said.
“Plus, the Dynamic motion takes all the material away in one simple, continuous, non-stop, uninterrupted cut. Not only does that make better parts faster—because it’s not lifting, stopping, and starting again—but it also extends the life of the tool.”
James also relies pretty heavily on the software’s tool library.
“The library gives me a starting point. I don’t 100-percent understand how to build tools. But, Mastercam has made it a lot easier. If I’ve got an end mill, I just pull it in and change a couple of numbers, instead of spending the extra five or 10 minutes building a tool. Plus, the tool is more accurately built in the software. And, of course, with a more accurately built tool, you make a more accurate part.”
Customer Quote
“The Dynamic motion takes all the material away in one simple, continuous, non-stop, uninterrupted cut. Not only does that make better parts faster—because it’s not lifting, stopping, and starting again—but it also extends the life of the tool.”
—James Nunn, Owner/Operator, Machine Nunn
Reseller Quote
“It was really sitting beside Jason (Parks) day after day that helped me. I had my own personal Mastercam teacher and I became ‘a sponge’. Everything Jason could show me, he showed me. Everything I could take in, I took in. Sometimes I’d get it the first time, sometimes it would take two or three tries; but I was persistent.”
—James Nunn, Owner/Operator, Machine Nunn, on Mastercam Reseller Barefoot CNC