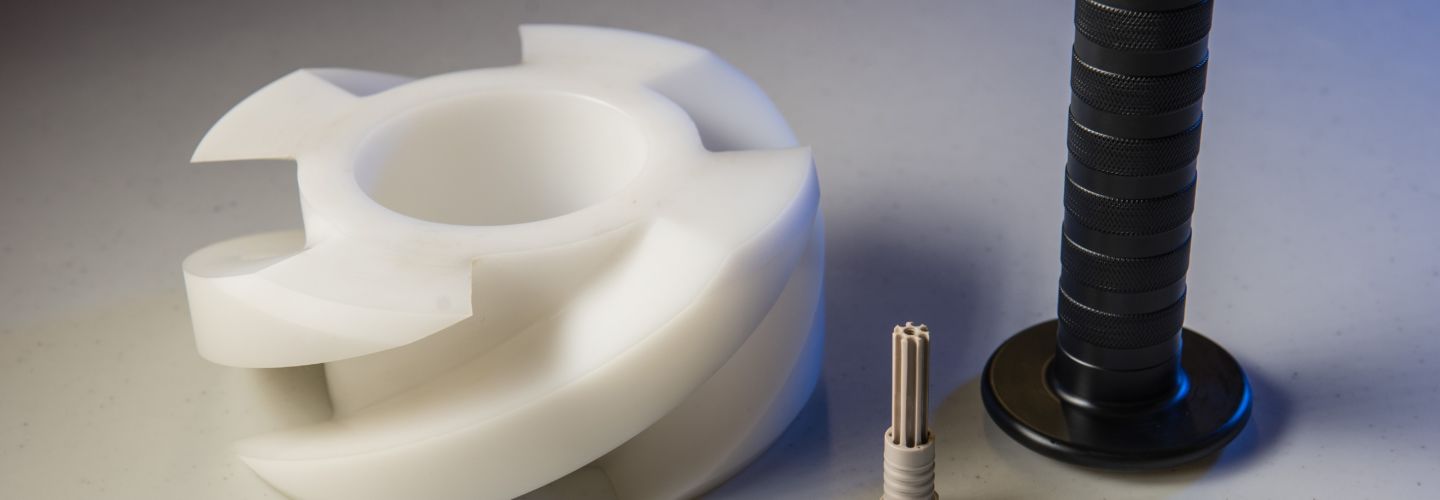
Setup and Machining Times Drastically Reduced For Custom Composite Component Shop
APS Plastics & Manufacturing (Tomball, TX) has been machining custom composite components since 2006. In 2016, the company was acquired by Framework Capital Partners, an investment firm committed to optimizing manufacturing practices. Led by CEO Mushahid (Mush) Khan, APS specializes in small high-precision components made of thermoset plastic composites, glass films, and other plastics measuring from 0.030” to 25” in diameter for inclusion inside valves, high-end electrical connectors, and insulators for the energy, medical device, and electronic device industries. The non-corrosive composites are suitable for harsh, corrosive environments.
Quick Facts
- Product Used: Mill, Lathe
- Industry: Plastics, Energy
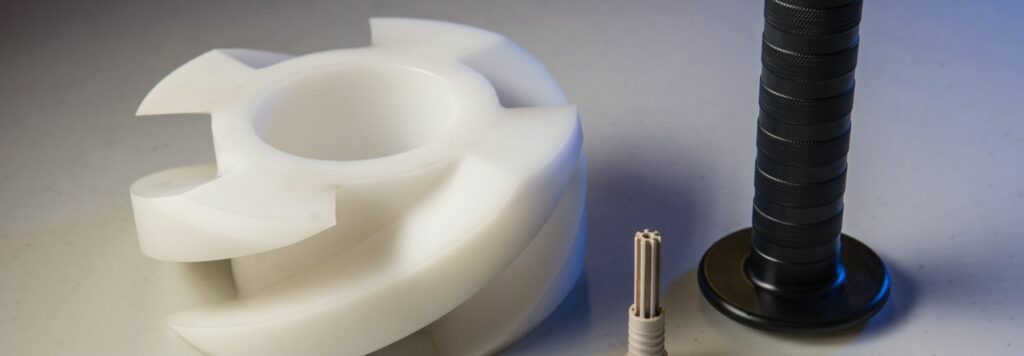
Project Details
- The Challenge: An energy customer needed help manufacturing a difficult to machine part made of Inconel®-covered tin and plastic. Long setup times, tool breakage, and problems with deflection and chatter push off needed to be addressed at the outset as they could complicate the process or render it impossible to do.
- The Solution: Mastercam, the most widely used CNC software for CAD/CAM operations.
- Benefits:
- Easy to learn for those machinists with limited computer knowledge
- Dynamic toolpaths allow machines to run at very high speeds without tool breakage
- Ability to build solid model templates reduces time when programming similar parts
- Programming Z-Axis in Increments Allows Machining Different Segments of the Same Part
APS Plastics & Manufacturing (Tomball, TX) has been machining custom composite components since 2006. In 2016, the company was acquired by Framework Capital Partners, an investment firm committed to optimizing manufacturing practices. Led by CEO Mushahid (Mush) Khan, APS specializes in small high-precision components made of thermoset plastic composites, glass films, and other plastics measuring from 0.030” to 25” in diameter for inclusion inside valves, high-end electrical connectors, and insulators for the energy, medical device, and electronic device industries. The non-corrosive composites are suitable for harsh, corrosive environments.
After the acquisition, Khan (who is an engineer) and his team analyzed manufacturing processes realized they could be even more efficient. He began working with consultant Rob Burton, who brought years of experience with Mastercam® CAD/CAM software and machining to look at everything to ensure they had optimized the processes as much as possible.
When Burton evaluated the APS shop, he first looked at programming and then manufacturing and found that the CAD/CAM software was not being used to its full potential. He credited its user-friendly interface with helping the team get up to speed quickly and alleviate fears of new technologies. “You have the ability to build templates inside of Mastercam so, if you have a family of parts that you’re programming, you can program one, export all of that out, save it, and re-import all of that information (i.e. toolpaths) to reapply to a similarly styled part, re-associate your geometry, and your program is done,” said Burton.
“We have taken the more powerful tools that are available in Mastercam and directly applied them to our programming strategies in our toolpaths to reduce cycle times and increase through put,” said Burton. “We recently purchased and implemented SOLIDWORKS® which works fluidly with Mastercam. When we make a change to a part, Mastercam, due to its change recognition with SOLIDWORKS, recognizes the changes in the model, updates inside Mastercam, and prompts us to accept or reject the new toolpath which cuts out the time in having to go back and reprogram that model from scratch.”
The team can take full advantage of the shop’s 7-axis Swiss and bar feed machine which, according to Burton, reduces set up time by about 70% and increases throughput by roughly 40%. They can switch from a Swiss-style chucker lathe to a fully automated bar feed lathe for short runs and high-volume runs. The machine does all milling and turning, including complex parts, in one operation, freeing up the shop’s five mills and five lathes for other work. According to Burton, all of their spindles are “maxed out” at 10,000 RPMs and are run “wide open”. Plastics are run at the maximum feed rates possible – between 400 to 1200 inches-per-minute – before the materials break down. On steel, the carbon-based material is cut around 600 inches-per-minute with high-performance end mills on the high speed machine. The software’s Dynamic Motion technology, which consists of high speed toolpaths programmed with proprietary algorithms that detect changes in the material as the tool moves through it, permits the tool to be constantly engaged with the material, significantly reducing air cuts and material damage. The tool plows through the material, making the faster speeds possible.
An example of this involves a global energy company based in nearby Houston that asked APS to machine parts they struggled to run internally. The part was molded over tin with some Iconel® on the end with the rest being PEEK material. “We were trying to cut Iconel and plastic at the same time, which is extremely difficult to do,” recalled Burton. “We worked with the customer directly in getting our manufacturing set up. By being able to implement the proper button tooling, we could cut both materials and limit the amount of deflection on the part which was a major problem when cutting from plastic, because all of a sudden, the tool becomes buried in the Iconel. There were several inherent problems with the chatter push off and tools breaking and we were able to eliminate all of those with the Dynamic toolpaths.” Additionally, the team used a feature found in Mastercam 2018 that allows machining along the Z-axis on a lathe in specific increments. Using this strategy, they turned an Iconel section, backed out, ran the Dynamic turning on the Iconel, then went back in on the other segment to machine the plastic out. “As we developed the tool, we needed to specify different variables in our software in terms of, if a whole diameter is X then you can use tools A, B, and C. So that way, when we populate that information into the window, it knows what tool to select in the background and apply to that part when it generates a toolpath. We already know that part is already loaded in the machine, we know the tool number and it matches across the board. We can take a part that would take somebody maybe half a day to program and literally program it in five minutes. And have the machine running before they even finished the program,” said Burton.
Customer Quote:
“As we developed the tool, we needed to specify different variables in our software in terms of, if a whole diameter is X then you can use tools A, B, and C. So that way, when we populate that information into the window, it knows what tool to select in the background and apply to that part when it generates a toolpath. We already know that part is already loaded in the machine, we know the tool number and it matches across the board. We can take a part that would take somebody maybe half a day to program and literally program it in five minutes. And have the machine running before they even finished the program,”
Rob Burton, General Manager, APS Plastics & Manufacturing