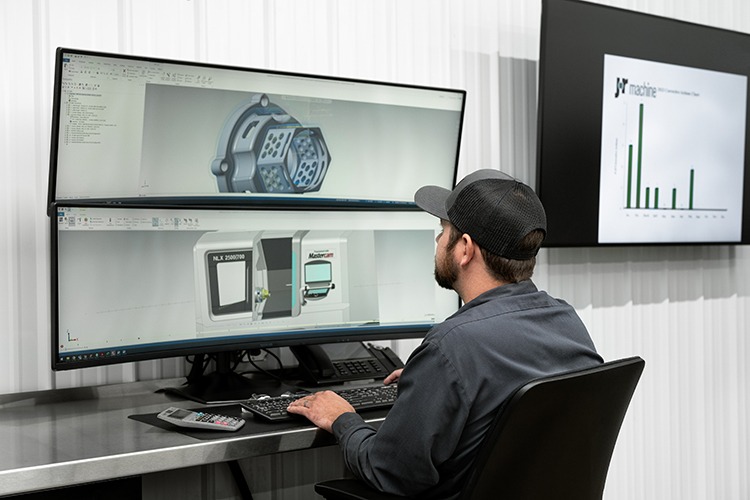
JR Machine Attracts Aerospace Customers with Advanced Mill-Turn Techniques
JR Machine increased its shop capabilities without updating any of its existing machines or installing new ones simply by upgrading its CAD/CAM software. In doing so, JR Machine reduced programming time and increased part quality.
The Challenge
Programming and cutting aerospace parts that require both milling and turning.
The Solution
Mastercam, the most robust CAD/CAM software for machining applications.
Benefits
- Advanced CAD tools make complete, accurate models of parts from vector-based drawings.
- Mill-Turn combines the best functions of both applications, reducing programming and machining time.
- Simulation, Backplot, and Verify visualize the machining process and identify possible problems.
- Dynamic Turning automates tool motions to run machines faster and more safely.
- 3 + 2 machining approaches allow users to apply some multiaxis techniques without having to upgrade software or equipment.
Project Details
JR Machine is a leading contract manufacturing company for complex precision machined parts. “We’ve really tried to target the aerospace industry, which requires highly complex parts,” said Shane Kunschke, JR Machine vice president of manufacturing. “That’s what drove us to purchase our Mastercam CAD/CAM software. We haven’t made any CNC machine upgrades, but our machines are now capable of doing this type of high-end work.”
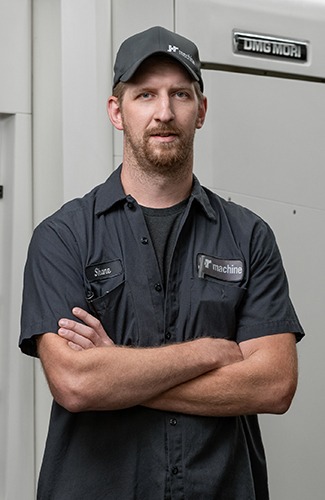
The CAD portion of the software renders the customer’s vector-based drawing to create an accurate and precise model of the part, complete with tolerances and surface finishes. Because JR Machine uses an integrated system, pulling the CAD file into its CAM interface takes no time and means no loss of data. Now, the company is able to work with whatever prints and models it receives.
In the case of complex aerospace parts, JR Machine was writing a workable CAM code but having to return to it often to hand-edit the G-code. Lead Programmer Brock Jaskolski shared that he found writing a mill program easiest, but had to tweak it to work with his lathes, essentially doubling his programming time and increasing operator error. Jaskolski knew his software could do better. He reached out to his certified local Mastercam Representative, ShopWare Inc. in Elgin, IL.
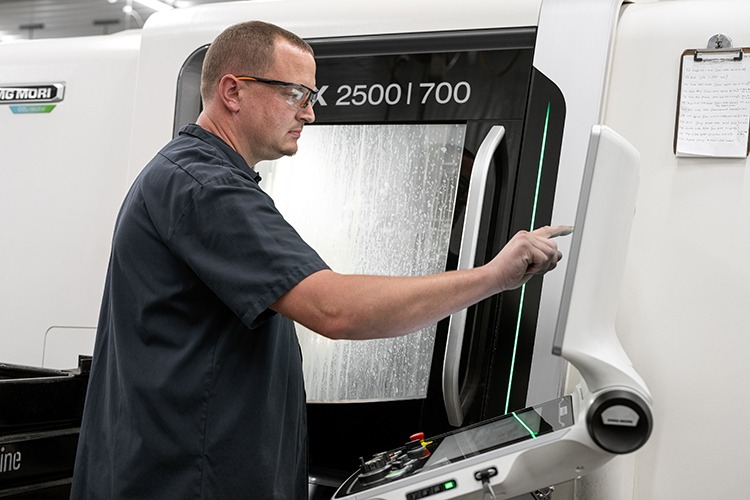
ShopWare Application Expert Todd Rathkamp was quick to suggest the software’s Mill-Turn solution, which harnesses the powers of milling’s tool rotation and turning’s workpiece rotation. Parts that previously would have been turned on a lathe and then milled can now be cut entirely on one CNC machining center with Mill-Turn. Productivity is greatly increased because multitasking CNC machines reduces multiple setups, manual part handling, redundant fixturing, and machine downtime.
Jaskolski relies heavily on the Mill-Turn product’s included simulation package. In addition to verification functions, the integrated simulation offers a digital twin of whichever machining unit is paired with a particular part. Jaskolski can load his program and watch it run in real-time on a detailed virtual representation of his CNC units.
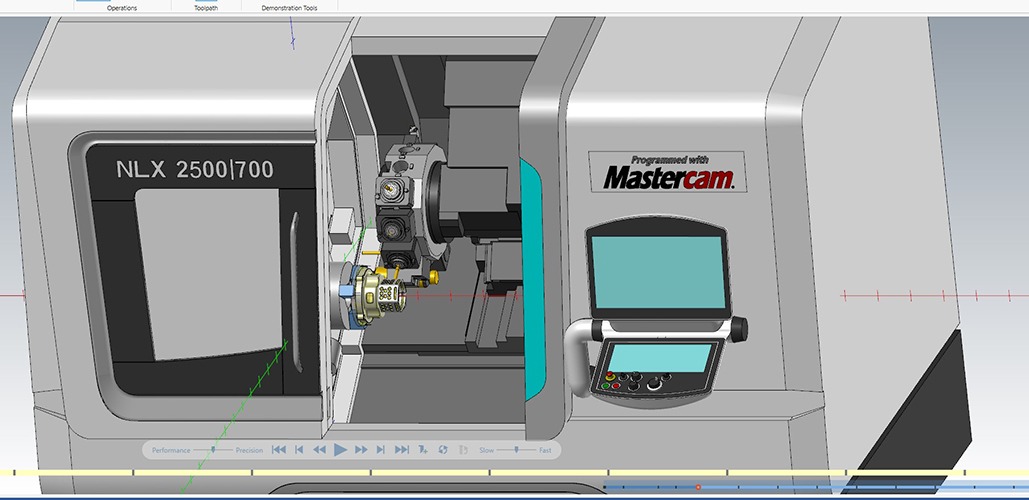
Another suggestion from the Mastercam Representative was Dynamic Turning, powered by Dynamic Motion Technology. Dynamic toolpaths are stock-aware and intelligent. During machining, a Dynamic Turning toolpath will adjust rotation speed, cutting angle, and tool depth to perfectly match the machining environment. Chip size will be optimized, materials and tools will be safeguarded, and the machine will be free to run faster than ever before.
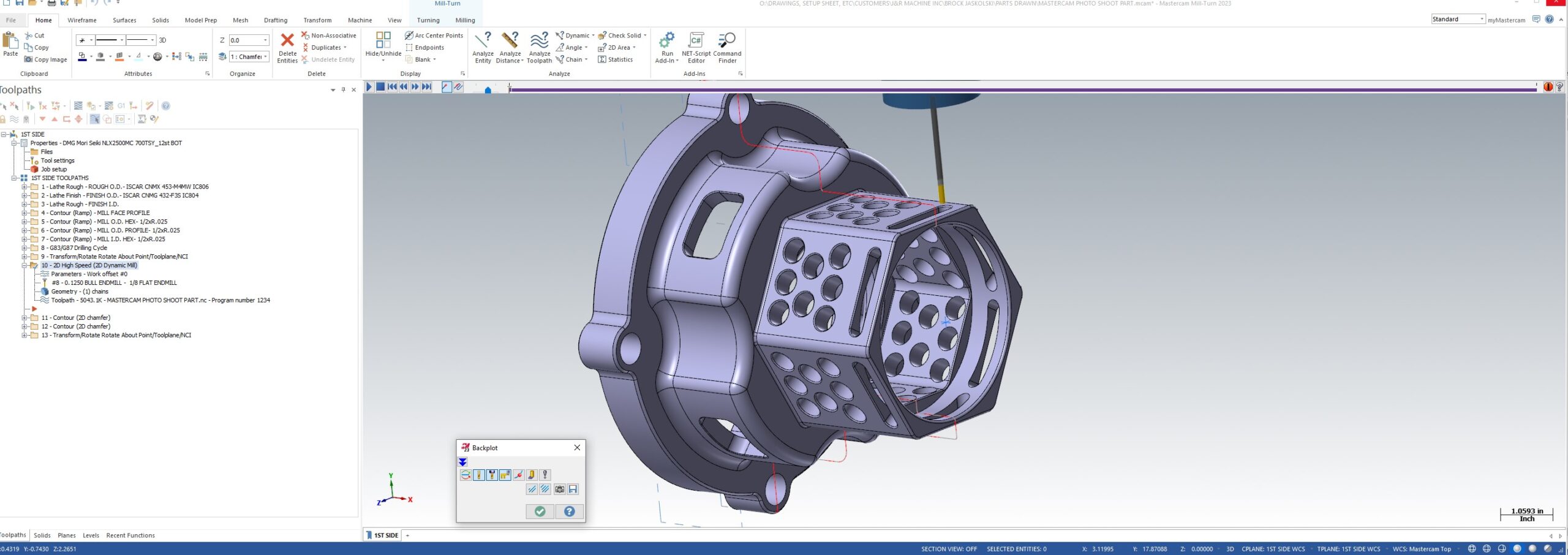
The parts the company takes on are becoming more and more complex. To meet this head-on, Jaskolski uses CAD/CAM software to simulate 3 +2 simultaneous machining. This style of machining harnesses the power of multiaxis machining within a 3-axis environment by tilting the tool held at a fixed angle. Using a successive sequence of orientations, users can mimic 5-axis simultaneous machining without going all-in on multiaxis.
Quick Facts
- Product Used: Mastercam Mill-Turn
- Industry: Aerospace
“Using Mastercam has really helped with training. Now, it’s much easier to get people up to speed. It’s hard to find experienced employees, so if Brock can program a part in the office and make it almost foolproof as it goes to the machine, it’s easier for an operator to comprehend what’s going on. The operator no longer has to massage the program or know exactly what every single line of code is doing.”
Shane Kunschke, Vice President of Manufacturing, JR Machine, Shawano, WI