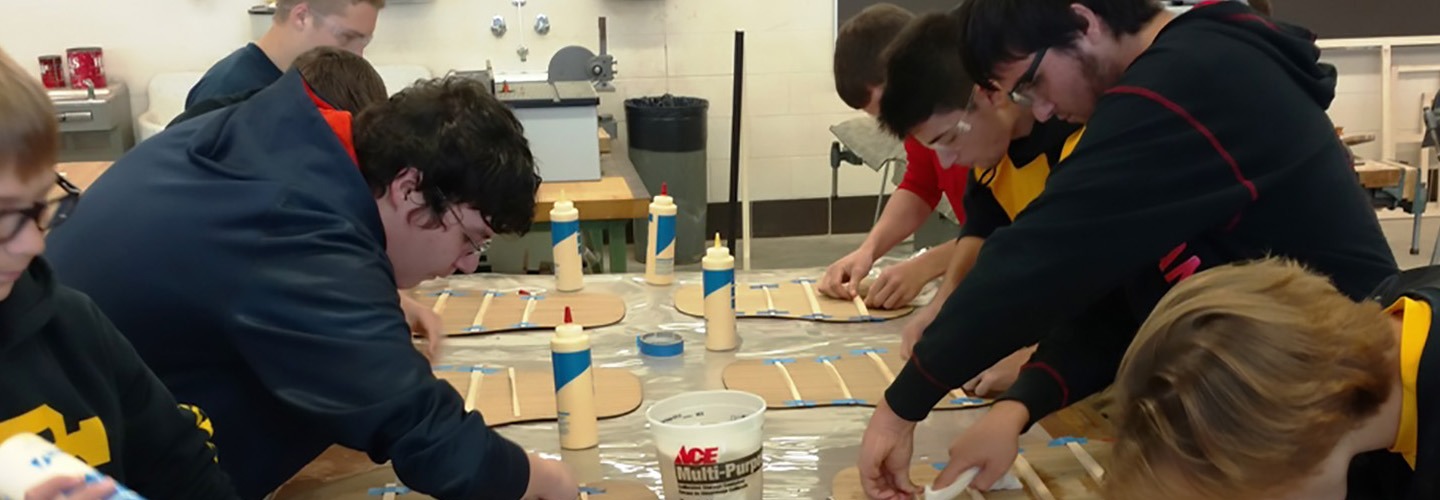
Guitars Hit the Right Notes at Reed-Custer
The Industrial Technology/Advanced Manufacturing Program at Reed-Custer High School in Braidwood, Illinois, is fortunate to have Mark Smith teaching the program’s students all the fine points of advanced woodworking. He has been a devotee of woodworking for many years, both in industry and in the classroom. To keep their interests up and give them skills in CAD/CAM that they will take with them after graduation, he has included the manufacture of beautifully crafted guitars in his curriculum.
Quick Facts
- Product Used: Educational Suite
- Industry: Consumer Goods, Education, Woodworking
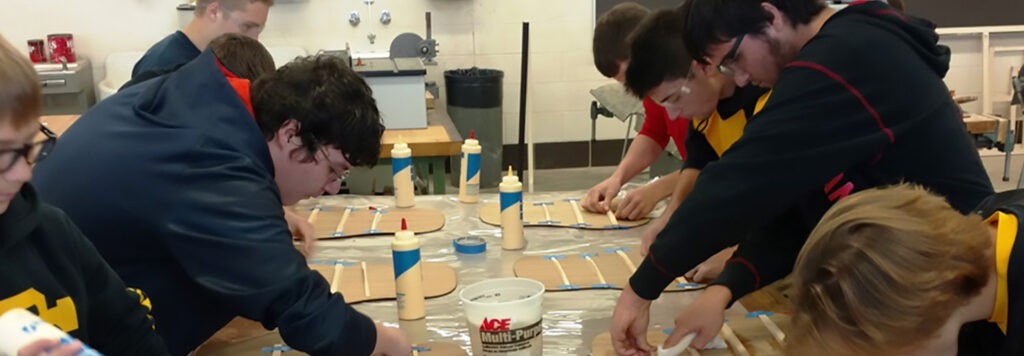
Project Details
- The Challenge: Employ the level of tool path software that would permit CNC machining of critical components in the neck of the guitar to result in proper tuning capability.
- The Solution: Educational Suite
- Benefits:
- Designed for a wide range of CNC machine tools
- Easy to teach to high school students
- Stepped in complexity for learning ease
- Assistance available for teachers as needed
Smith immerses his Reed-Custer High School students in hands-on operations, a learn-by-doing method that helps them gain confidence in performing each step required to bring pieces of wood into a beautifully finished product. In addition to stressing repetition to build confidence, Smith also promotes variety in student projects to encourage interest in his program. His classes have created wood frames for the sunglasses industry, skateboards for pleasure, kitchen cabinets for neighbors and even professionally finished guitars for themselves and family. Facilities for the program include a classroom with 16 seats of Mastercam® for programming CNC tool paths, a room for assembly of various projects and a shop that is filled with traditional woodworking tools and a Thermwood® Model 43 CNC router.
“Our freshman students start out with Orientation to Technology where they begin by learning all the safety rules for handling the equipment they’ll find in a typical shop and then proceed to basic CAD/CAM operations,” says Smith. “I let them design logos and artwork for long boards that they will demo with pride at the skateboard parks and show them how to transfer the designs into Mastercam to program the CNC router. The student checks each piece of geometry using Mastercam’s chaining option that has the software examine their design, one chain at a time. They’re checking for things like double entities because when kids are learning to draw, they often put geometry on top of geometry. They do quite a bit of work in ‘cleaning up’ their geometry, making sure corners are correct and that lines do not overlap or fall short.”
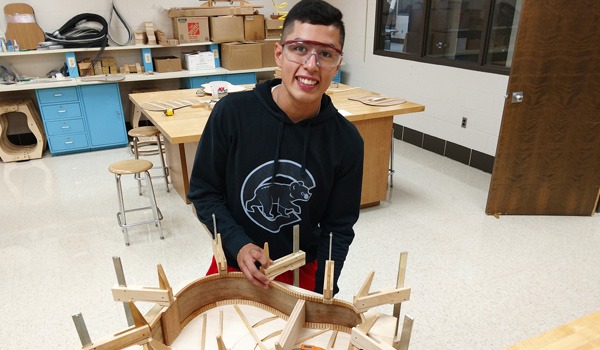
As sophomores, the students can take a guitar-making course called STEM I. The acoustic guitar materials are provided to the class by Taylor Guitars®. In the process of building their guitars, the students learn how to work with hand tools and power tools, along with more advanced operations using Mastercam and the CNC router. “Taylor Guitars contacts me in advance to find out how many students will be in next year’s class,” says Smith. Then, in August, they deliver shrink-wrapped pallets of guitar components to the school. There will be cartons with sides, backs, tops, bracing, kerfing, necks, ebony fret boards and so on, all roughed out and ready for hand- and machine-finishing and assembly.” Students pick out the components that strike their fancy. One of the choices is mahogany, while others are more exotic, such as ovangkol, and each has its own distinct grain design, with no two alike. This allows each student to build a guitar that is unique to his or her personal taste.
“While we are building these guitars, we have the students in a classroom at least once a week for math lessons,” continues Smith. “Even though most high school students wouldn’t be able to do the kind of math needed to determine where the metal frets go in the neck of the guitar, we show them the math and how it works to create an instrument capable of such pleasant music. It’s a little mind-bending for them to watch all these calculations going on in the video presentations, but they realize that because somebody knows how to do the math, we have these awesome guitars. They see the value in learning math, from basic arithmetic all the way up to, and including, advanced algebra equations. We’re also exposing them to the science behind abrasives, finishing, wood preparation and all the steps that go into a fine wood product.”
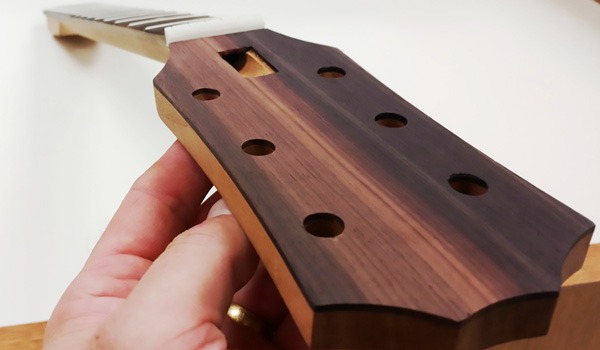
Students use a special jig and router tool to prepare a space all around the face and bottom of the body, where they meet the sides, to receive an attractive edging material that hides the structural member slots and give the body a finished ‘look’. “We built our own humidity chamber for the guitar bodies to reside while we work on the rest of the components,” says Smith. “It keeps the interior of the chamber at between 35% and 50% relative humidity because the thin wood of the bodies might crack if subjected to the 20% humidity of our Midwest climate during the winter before the guitars are finished.”
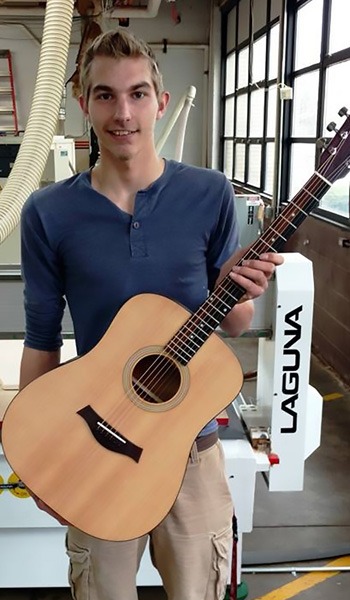
An important function for Mastercam and the router is to machine the opening in the neck of the guitar that allows access to the truss rod so the guitarist can adjust it with an Allen wrench to compensate for changes due to age, humidity, and other variables that affect tune. The oval opening is sealed with an attractive cover. The fret board is then glued on using the registration points as a guide and the back of the neck, along with the tuner holes, is machined to precise specifications. “These are operations being assigned to Mastercam and the CNC router,” says Smith. “The more we can do using automated manufacturing processes, the more time we can spend teaching the various sciences that deal with woodworking, whether it be for guitars or any of the many other projects we have our students doing. I’ve been including guitars in my woodworking program for the past eight years both here and in other schools, so there are a lot of kids that have benefited from this course. I have to thank Taylor Guitars, Mastercam, Thermwood and the dozens of manufacturers who contribute supplies and advice to our program every year. Our graduates are well prepared to tackle a wide range of manufacturing operations and companies, both large and small, are inviting them onto the payroll.”
“Our graduates are well prepared to tackle a wide range of manufacturing operations and companies, both large and small, are inviting them onto the payroll.”
Mark Smith, Industrial Technology Program Teacher, Reed-Custer High School