Mastercam Mill is fully associative CAD/CAM for 2 1/2- to 5-axis machining and delivers streamlined mill programming and toolpaths powered by Dynamic Motion® technology. Mastercam 2025 is here to elevate your machining experience with powerful toolpaths, flexible tool motion, and our most intuitive interface yet. Here are some top Milling features—and how they can help your shop.
1. Mastercam Deburr
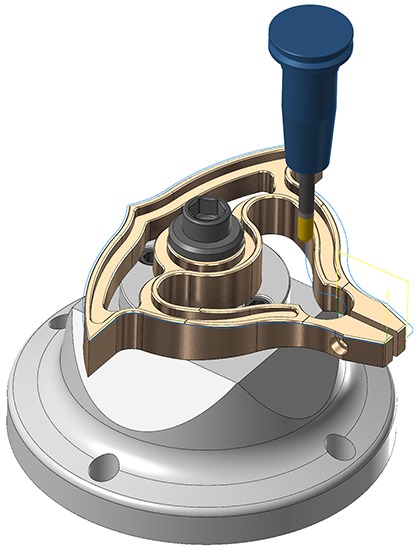
We are excited to announce the release of Mastercam Deburr, the ultimate solution for efficient and precise deburring. The Mastercam Deburr Add-On offers significant advancement for users of Mastercam 2D and 3D Milling, Mastercam Router, and Mastercam Mill-Turn.
This advanced solution features automated edge finishing which streamlines the deburring process, enabling precise control and minimizing the need for manual finishing.
Mastercam Deburr tackles complex edges on non-prismatic shapes with ease, and automates complex deburring tasks, saving valuable time and greatly enhancing the quality of the final product.
Mastercam Deburr simplifies deburring with automatic edge detection and intuitive controls, ensuring a faster and more accurate deburring process.
2. Finish Passes
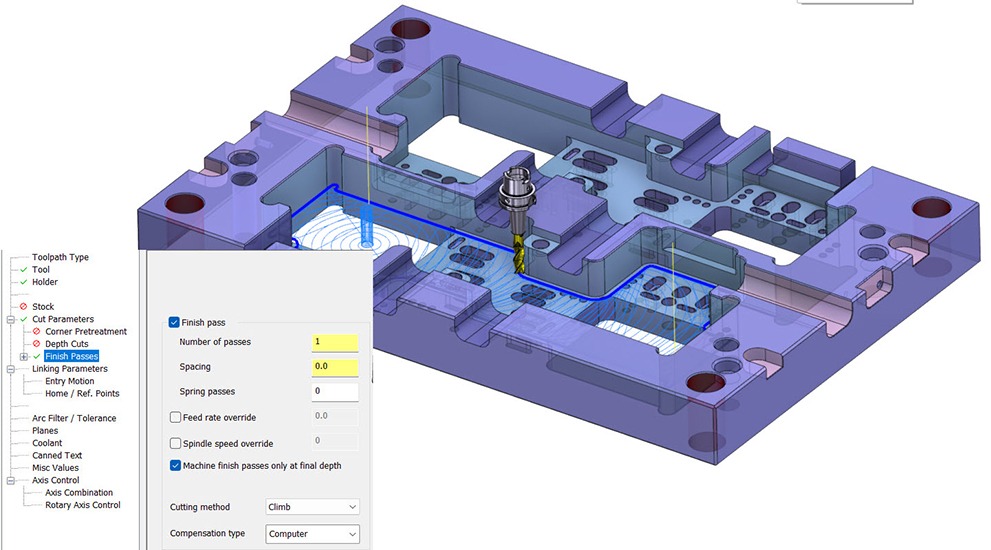
Mastercam 2025 introduces the ability to add Finish Passes to 2D Dynamic Mill and Area Mill toolpaths.
Use the new Finish Passes page to add high speed finishing passes along the selected boundaries of the toolpath. After selecting the Finish pass option, use the other parameters to further define the finish pass, such as feed rate and spindle speed overrides.
Use Spacing options to ensure there is material for the finish passes and use the new Lead In/Out page to set specific lead in and out options for finish passes.
3. Solid Hole Selection
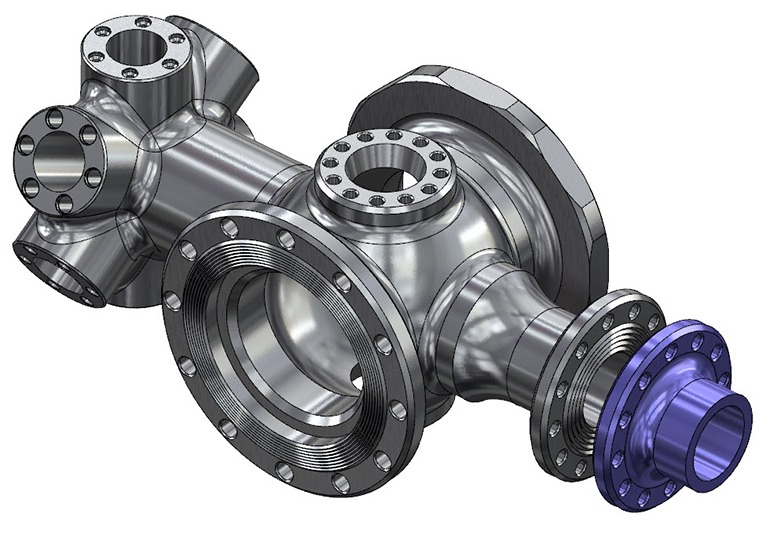
Mastercam 2025 introduces significant enhancements to the Solid Hole Selection feature, which is integral for those utilizing Hole Making and Process Hole toolpaths. The changes associated with this update create a more efficient, precise, and controllable hole selection.
The Solid Hole Selection update encompasses many new behaviors for selecting holes such as simplified selection rules, multiple hole types are allowed in a single toolpath, and segment selections from the same hole are always joined together into a single feature. Other features include solids history selection and selection across multiple solid bodies, as well as a unified selection experience when working with native Mastercam solid hole features or imported neutral CAD formats.
4. Thread Milling Features
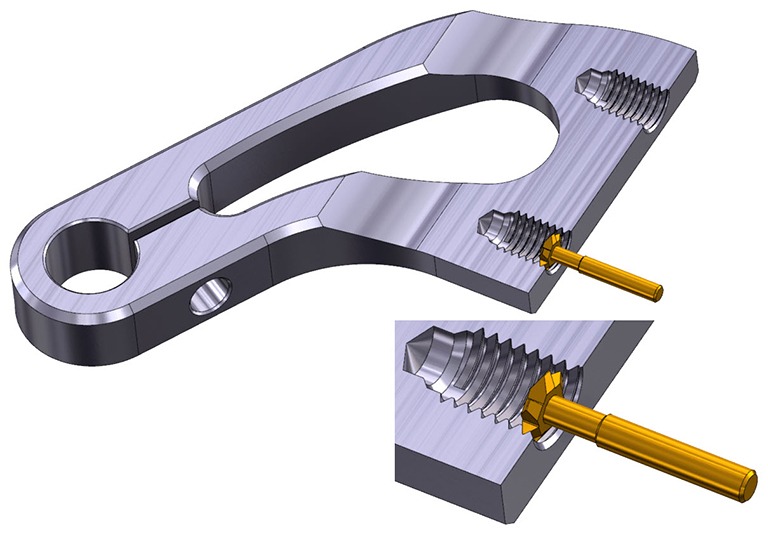
Cutter Compensation Moves: Thread Mill now features the new Plunge after first move and Retract before last move parameters. These parameters define, optionally through the Line lengths fields, a linear move at the feed plane that occurs before and after the cutter engagement. This means you can define the linear motion outside of the machining area for enabling and disabling cutter compensation. The Line length fields specify the length of the linear moves.
Often when using thread mill tools, the tool diameter and the diameter of the hole being machined are close in size. This means it is not possible to move the tool linearly before engaging in the cut, as required by most machines when enabling and disabling cutter compensation. Use the Plunge after first move and Retract before last move parameters to solve this problem.
Directional Cutting: The new Cutting Direction and Spindle Direction fields found on Thread Mill’s parameter page not only increase visibility, but also provide better control over the cutting direction due to the influence of the Tool page’s Spindle direction parameter on the cutting direction.
Lead In/Out Options: New options in the Lead In/Out page add tool manufacturer-recommended helical functionality. The new options also provide control over cutter compensation and overriding entry speeds and feeds.
Line Length Controls: When you enter values in the new Line Lengths controls, Mastercam constructs a line perpendicular to the entry and exit moves. You can also use this feature to enable and disable cutter compensation outside of the diameter to be machined. You would apply this where the hole diameter is too small for the moves to take place within the machining area.
Tool Edge Feed Rate: Use the new Tool Edge feed rate checkbox to calculate the feed rate based on the tool’s tangential edge rather than on the centerline. Tool edge feed rate produces a more accurate feed rate based on the cutter diameter and the diameter of the hole being machined. It also allows you to program Thread Mill operations with a higher level of accuracy, which helps achieve proper tool wear and a more efficient toolpath. Save time by automatically calculating the proper feed rate for Thread Mill, rather than the need to manually calculate the feed rate at the edge of the tool’s diameter.
Want More Information?
If seeing the top Milling features has you ready to update or you want to learn more about what Mastercam can do for your shop, please reach out to your local Mastercam Representative. Or, if you’re ready to explore Milling features on your own, download the free Mastercam Learning Edition.